What Is the Process of Commissioning?
Today’s buildings are equipped with increasingly complex and interconnected mechanical and electrical systems. While these systems grow, the expectations of building owners, occupants, and regulatory bodies continue to escalate, which drives the demand for thorough commissioning services.
Have you ever wondered how large, complex projects are commissioned and initiated?
Although each project requires a tailored plan to achieve its unique objectives, the overall process for planning, commissioning, and starting up a project follows a consistent framework to ensure success.
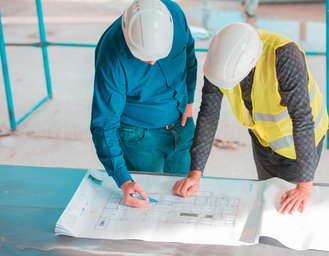
The Role of Commissioning
Commissioning confirms that systems are properly installed, thoroughly tested, and prepared for safe, efficient operation. It ensures each component aligns with design specifications and regulatory standards, reducing risks and enhancing performance. By following a structured approach, commissioning ensures systems are optimised and compliant before they enter service.
Commissioning also plays a key role in identifying potential issues early, allowing for corrections before systems go live. This proactive approach can prevent costly downtime or operational inefficiencies in the future. Additionally, commissioning provides valuable documentation and reporting, which aids in future maintenance and troubleshooting efforts.
What Are The Steps Of Commissioning?
On a hyperscale data centre or a national power grid, the commissioning process guarantees that everything functions as intended, from basic mechanical systems to complex automated controls. Although each project has unique features, the commissioning process follows a consistent series of stages that ensure efficiency, compliance, and safety.
Let’s take a closer look at the steps that will give us a better understanding of what is involved in the commissioning process.
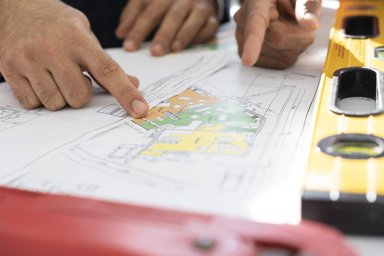
Step 1: Planning (Pre Construction)
The success of the commissioning process depends largely on thorough planning, which begins long before equipment arrives at the site. In this phase, every detail of the commissioning activities is organised, roles are defined, and safety protocols are established.
The important elements of planning are the following:
Schedule and Milestones: Commissioning schedules are developed alongside construction timelines to ensure that both teams are working towards the same goals. This approach guarantees the project moves forward in an organised, step-by-step fashion.
Team Formation: The commissioning team is formed early and includes electrical, mechanical, and automation leads, as well as contractors and consultants. Involving the owner’s operations team at this stage is important so they can become familiar with the systems they’ll eventually manage.
Documentation, QA/QC, and Safety Measures: Preparing test plans, procedures, and drawings in advance helps to streamline the commissioning process. This includes the review of RED TAG and Compass documentation, which focuses on equipment documentation review and QA/QC inspections of installed equipment before testing begins. To ensure safe working conditions, safety protocols, such as Lock Out Tag Out (LOTO), are also implemented.
Thorough planning ensures that all team members know their responsibilities and that the commissioning process can proceed efficiently.
Step 2: Factory Acceptance Testing (FAT)
Before equipment is installed on-site, it undergoes Factory Acceptance Testing (FAT) and Level (Lv2) Testing to verify that it meets design specifications and functions correctly. This step helps to catch any potential problems early and reduces the risk of delays once the equipment is installed.
FAT checks that the equipment meets all the necessary design criteria, including control systems and protection circuits. In complex projects, interfaces and systems are tested in simulated environments to validate that they will function correctly once integrated on-site. FAT allows teams to address any equipment issues before installation, ensuring a smoother commissioning process later on.
Meanwhile, Level 2 (Lv2) Testing is also carried out during this phase to verify that the single-phase, three-phase, and control systems function as intended, as dictated by client requirements. Lv2 Dead Testing ensures all equipment meets safety and operational specifications before being sent to the site.
By incorporating FAT and Lv2 testing, the commissioning team can address any equipment issues early, ensuring a smoother commissioning process later on.
Step 3: Mechanical Completion
Mechanical completion marks the point at which construction is finished and the system is handed over to the commissioning team for testing. This phase ensures that all systems are installed as planned and are ready for the detailed commissioning process to begin.
Some activities that involve mechanical completion are:
- Walkthroughs and Deficiency Tracking: A walkthrough of the installation is conducted by both the construction and commissioning teams to identify any deficiencies. Critical issues such as non-compliance with design specifications and electrical and control system issues among others are addressed before proceeding to the next phase.
- System Checks: The team verifies that major components like valves, wiring, and auxiliary systems have been installed correctly and are ready for testing.
- QA/QC Inspections: At this stage, QA/QC inspections continue to play a key role in ensuring all systems comply with the required standards before moving forward.
Step 4: On-Site Commissioning
On-site commissioning begins when mechanical completion is verified. This phase tests the equipment in its final installed environment to confirm it operates as intended.
- For mechanical systems testing, pipes are flushed, pressure is tested, and rotating equipment like pumps undergo initial tests to verify their performance.
- For electrical systems, panels are energised, and communication lines are tested to ensure control systems are functioning. Protection systems and transformers are calibrated, with Level 3 (Lv3) testing ensuring energised equipment scripts are followed to maintain system safety.
- Testing Documentation: During this phase, detailed testing documentation is created and maintained. This includes CX schedules, RED TAG documentation, Lv2 Dead Testing schedules, and Lv3 Startup scripts (CFCI), which serve as critical records for tracking progress and compliance.
For example, GCL, an engineering service provider specialising in commissioning management for data centres, provides comprehensive on-site commissioning services across the EU and UK regions.
GCL’s scope includes SAFE isolation, energization, Lv2 Dead Testing, Lv3 Live Testing, and daily QA/QC and client observation reports, ensuring efficient and safe systems integration for hyperscale data centre operations. Their expertise in turning around projects behind schedule and budget demonstrates the importance of skilled commissioning teams in maintaining high safety and operational standards.
Step 5: System Startup
Once on-site commissioning tests are complete, the system is ready for startup. System startup is a required milestone in the commissioning process, as it brings all components online for the first time, ensuring smooth, stable operations.
In this step, the equipment and processes are fully activated and tested under real-world conditions.
The system startup procedures begin with the mechanical and electrical ramp-up. As systems are started gradually, mechanical flows and electrical power levels are carefully monitored to confirm that they do not exceed operational limits. Next, the automated systems are put through fault-testing scenarios to ensure they can respond to unexpected conditions effectively.
Step 6: Performance Validation
With the system now operational, the commissioning team moves into the performance verification phase. In this phase, the focus shifts to ensuring optimal performance to meet long-term project goals.
Depending on contract requirements, the system may need to operate continuously for a set period (e.g., 24 hours or 30 days) without any major issues. Then, key performance indicators (KPIs), such as efficiency and load capacity, are closely monitored to ensure the system meets all operational criteria. Once verified, a Provisional Acceptance Certificate (PAC) is issued.
Step 7: Operational Preparedness
The final phase of commissioning ensures that the owner’s team is fully prepared to manage and operate the system. This phase guarantees a smooth handover from the commissioning team to the owner, with all systems ready for reliable, long-term operation.
This step includes:
Operator Training: The owner’s operations team is trained on the new systems, ensuring they are well-prepared to manage day-to-day operations and respond to any issues.
Handover of Documentation: Comprehensive documentation is provided, detailing system layouts, maintenance schedules, and warranty information. This helps the operations team have the necessary resources to maintain the system for long-term use.
Step 8: Support for Client Commissioning Agent (CXA) Activities
The final step in the commissioning process is providing support for CXA activities to ensure the long-term reliability of the systems.
In addition to managing the commissioning process, Data Solar CX supports the Client Commissioning Agent (CXA) during the later stages of the project, particularly for Level 4 (Lv4) and Level 5 (Lv5) activities.
- Support for LV/HV Switching Activities: Data Solar CX aids in Low Voltage (LV) and High Voltage (HV) switching activities, ensuring compliance with site-based electromechanical safety rules and local statutory guidelines.
- Permitting and CX Coordination: The team assists with the execution of compliant permitting systems, ensuring safety and efficiency in line with the client’s operational protocols.
- Coordination with CXA: Collaboration with the CXA involves supporting SAP/AP switching and energisation efforts to ensure the successful integration of systems into operational workflows.
Ensuring Project Success Through Expert Commissioning
Commissioning is a comprehensive, multi-phase process designed to ensure large-scale projects are completed safely, efficiently, and in full compliance with all required specifications. Each step, from planning and testing to performance verification and operational readiness, guarantees that the system operates smoothly and meets project goals.
For more information on how commissioning can optimise your systems and improve project outcomes, contact our team at Data Solar CX. Our experienced engineers and technical professionals are committed to helping you reduce risk, address critical issues, and deliver cost-effective solutions to enhance your facility's performance. We focus on efficiency and sustainability, ensuring a positive outcome for your facility's operations and its occupants.