Top 10 Electrical Safety Tips In The Workplace
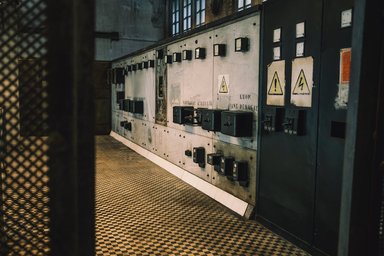
Electrical systems are fundamental to modern workplace operations, enabling everything from digital infrastructure to industrial equipment. These systems, while essential, present significant hazards, including severe electrical shock, thermal burns, and potential loss of life when improperly managed. To mitigate these risks, it’s important for all personnel to be aware of electrical safety tips that can help minimize dangers.
Professional electrical work requires specialised certification, yet all personnel should understand fundamental safety principles. This guide outlines critical electrical safety tips for workplace protection.
What is Basic Electrical Safety?
Electrical safety covers the practices and procedures that prevent injuries from electrical systems. All personnel involved with electrical work need to understand safe practices around electrical equipment. This includes adherence to organisational safety protocols and appropriate delegation to qualified technicians. The following electrical safety tips can be used to execute electrical safety at work.
Electrical Safety Rules
1. Assume All Electrical Parts as Live
Consider all electrical components energised unless verified otherwise through approved testing procedures. You can’t always see if a circuit is live, so always test before assuming it’s safe. Before working with or around any electrical equipment, using a calibrated testing device, such as a voltage detector, verify if a circuit is de-energized before setting your team to work.
This conservative approach is critical because electrical systems can appear safe when, in fact, they are still carrying a dangerous current. For example, residual energy or improper isolation can pose significant risks. By assuming that all components are live, you reduce the likelihood of accidental or indirect contact, which can lead to severe injuries or even fatalities. Always verify with and follow site based safety procedures before proceeding with any work.
2. Maintain a Safe Distance from Energised Components
In environments containing combustible materials, only electrical equipment specifically engineered and certified for these conditions should be used. Qualified personnel must verify power isolation before operations commence in potentially explosive atmospheres to prevent ignition events.
3. De-energise Equipment and Apply Lockout/Tagout
Prior to maintenance activities, implement complete power isolation. Utilise established lockout/tagout procedures to secure power sources and prevent unauthorised reactivation. Personnel must thoroughly understand and implement organisational lockout/tagout protocols without deviation, ensuring that risk and method statements (RAMS) are understood, signed onto by all members of the working party and complied with.
For example, consider a maintenance team performing routine service on industrial equipment. The absence of proper Lockout/Tagout procedures creates a scenario where unskilled personnel could inadvertently energise the plant and or machinery, exposing maintenance staff to live electrical components and risking severe injury.
The implementation of Lockout/Tagout procedures which include physical disconnection, separation and security of all sources of energy from the point of work, ensure isolations achieve safety from the system, the permit to work system and clear warning / LOTO tags ensures power restoration occurs only when, work is complete, conditions are verified and Personnel are aware of the new state of the system.
Comprehensive understanding and strict adherence to organisational Lockout/Tagout protocols are mandatory, as these procedures establish and form part of the safe systems of work that safeguard personnel against hazardous energy exposure.
These established safety measures protect personnel through systematic power isolation, compliant documentation and clear communication protocols.
4. Handle Electrical Equipment Safely
Proper handling of electrical equipment is significant to maintaining safety in the workplace. Some fundamental practices include;
- Confirm all members of the working party are trained and competent to operate the equipment.
- Regularly inspect equipment for defects and avoiding the use of damaged equipment.
- Always protect trailing leads and secure them for works of long duration.
- Ensure equipment is in date for calibration and has the correct tag signed by local health and safety management.
- Ensure the equipment is correctly rated for the activity you are undertaking.
These small steps can go a long way toward preventing accident and incidents.
5. Keep Conductive Tools and Cleaning Materials Away from Electrical Components
In any area where electrical hazards exist, always assume that electrical components are live. When working on or adjacent to energised equipment use non conductive tools or materials to protect against direct contact.
Additionally, take caution with cleaning supplies, as many solvents and materials like steel wool are conductive. Always keep such products far from live electrical parts to avoid accidents.
6. Use Physical Barriers to Protect Against Electrical Hazards
Physical barriers are an effective way to protect employees from electrical dangers, demarcation of work areas (DWA) is a critical step in preparation of the work area. Ensure that all cabinet doors on live electrical panels are closed to prevent access to live conductors or loop components. When barriers aren’t available or possible due to environmental conditions, such as when an electrician is performing maintenance or a technician is commissioning, use approved shields, signs, flashing beacons and warning markers to keep others away from the hazard and outside of the DWA.
The area should also be free of any obstructions to ensure quick access if necessary, maintaining general safety forms part of the competent person responsibly to the working party.
7. Be Cautious of Overhead Electrical Lines
Electrical dangers aren’t always on the ground. Personnel conducting elevated operations must maintain constant awareness of overhead electrical conductors as over head conductors can range from LV - 400kV where the voltage can bridge.
Always the maintain safety distance from exposed electrical conductors. This prescribed distances found in your site based safety rules, prevents electrocution, burns and arc flash incidents that may be presented with energised systems during elevated operations.
8. Avoid Using Electrical Equipment Near Flammable Materials
Electrical equipment must never be used in areas where flammable vapours, gases, or dust are present unless it is specifically designed for such environments. Ensure that qualified and authorised personnel have achieved safety from the system before working with potentially combustible materials. Taking additional precautions alongside COMPEX guidelines minimises the risk of ignition and explosion. When working in potentially explosive environments all personnel should be suitably trained and competent to understand the risks associated.
9. Follow Your Company’s Electrical Safety Protocols
Each organisation AND industry maintains specific electrical safety protocols electromechanical safety rules, controls of hazardous energies as examples are tailored to the operational environment and risk profiles.
Strict adherence to these established protocols is imperative for collective workplace safety and regulatory compliance. These directives form the foundation of a comprehensive electrical safety program and require consistent implementation by all personnel.
How Can You Identify Electrical Hazards in the Workplace?
Recognizing potential electrical hazards is the first step to ensuring a safer workplace. While electrical system deficiencies may not present obvious indicators, specific conditions warrant immediate assessment:
- Deterioration of conductor insulation
- Exposed electrical conductors
- Intermittent FAULTS or irregularities
- Earthing Connection point degradation
- Thermal or potential discharge indicators
Providing electrical safety tips and implementation of systematic workplace inspections enables preemptive hazard identification and mitigation. Upon detection of electrical system anomalies, execute the following protocol:
- Document the precise location and nature of the vulnerability
- Notify designated electrical safety personnel SAP / AP
- Implement appropriate access restrictions
- Maintain established safety perimeters until qualified personnel complete inspection and necessary repairs
This methodology ensures consistent hazard identification and appropriate response procedures while maintaining operational safety standards.
Achieve Workplace Safety with Specialised COHE Training
DSCX’s specialised COHE safety training programs offer comprehensive solutions for organisations looking to improve their electrical safety protocols.
From pre-contract award briefings to on-site delivery, we ensure your team is well-equipped to minimise risks and maximise efficiency. Our tailored training programs help establish a culture of safety excellence across your organisation.
Whether you're preparing for tender awards or facing site-specific challenges, we provide the practical tools and insights needed to prioritise safety. Contact us and learn more about our specialised COHE Safety Training and start building a safer work environment today.