Understanding Safe Systems of Work
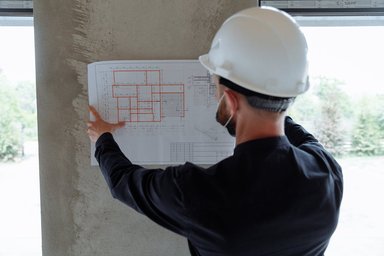
We've all heard the workplace safety stories, the near misses, the close calls, and unfortunately, the accidents that could have been prevented. While it's easy to view these incidents as "just part of the job," the reality is that most workplace accidents can be traced back to gaps in safety training and systems.
Safe Systems of Work play a critical part in taming workplace hazards by creating clear, practical blueprints for task completion while keeping worker protection in the foreground. Yet, developing these systems is only the beginning, organisations must regularly review and update their safety protocols to safeguard employees. This ongoing commitment to maintaining and improving safety measures ultimately strengthens the entire organisation's culture of proactive risk management.
This article will look into what defines a Safe System of Work, why it's essential to involve employees in its creation, and how businesses can develop an effective SSoW to minimise workplace risks.
What Are Safe Systems of Work?
A Safe System of Work provides a comprehensive shield against workplace accidents. Through methodical risk assessment, it examines every task for potential dangers. Industrial settings demand particularly rigorous implementation of these systems - from a facility's initial blueprint to its daily operations and beynd. By deploying specialised tools like Hazard and Operability studies (HAZOP), teams can spot and neutralise risks long before they pose any real threat to workers.
An effective SSoW requires strict adherence to established safety protocols, regular assessments, and documentation to meet regulatory compliance and demonstrate a commitment to workplace safety. This documentation may take the form of written safety policies or procedures, tailored to fit the specific needs of a business and its employees.
Why Involve Employees in Developing Safe Systems of Work?
Creating an SSoW is not just a top-down process; it involves collaboration with employees who encounter workplace hazards directly. Engaging workers in this process is critical for several reasons:
- Insight into Operational Hazards: Employees provide valuable input on potential hazards and operational risks, especially those unique to specific tasks or equipment.
- Compliance with Regulations: Many health and safety laws require employers to consult with workers when developing safety protocols.
- Improved Safety Culture: Involving employees fosters a culture where safety is everyone’s responsibility, leading to more proactive hazard identification and risk mitigation.
Steps to Developing a Safe System of Work
Once developed, the system must be implemented with accuracy. Continuous monitoring reveals opportunities for enhancement, while dedicated oversight ensures its effectiveness. These elements work together to nurture and sustain a proactive safety culture.
Here are some fundamental steps to guide this process:
- Revisit Employee Roles
Evaluate job roles and tasks to identify those with higher risk levels. By understanding each role’s risk profile, you can prioritise safety measures, focusing particularly on tasks involving maintenance, equipment handling, or construction—which are common areas of heightened risk. - Assess Risks and Hazards
Once hazards are identified, conduct a complete assessment to determine their origin and contributing factors. Consider the likelihood of an incident and its potential severity, which will help prioritise control measures. - Develop Control Measures
Brainstorm and implement control measures to address the identified risks. Controls may range from engineering solutions, such as equipment modifications, to administrative procedures like safe work practices and restricted access to certain areas. Industry standards and codes of practice provide benchmarks for minimum safety requirements. - Implement the System
After developing the control measures, implement the system across the workplace. This stage involves employee training, updating documentation, and ensuring that all staff understand their responsibilities within the SSoW framework. - Continuous Monitoring and Improvement
Even the most comprehensive safety system needs regular monitoring to stay effective. Monitor control measures, track incidents, and continuously seek improvements to the system. Regular reviews are particularly important after incidents, changes in procedures, or shifts in regulatory requirements.
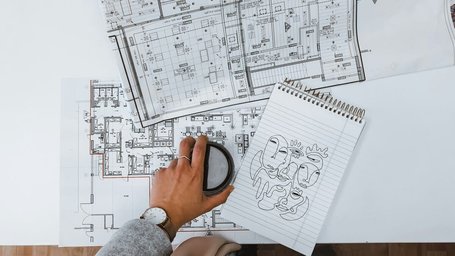
What Is an Example of a Safe System of Work?
Standardising safety practices can be especially beneficial for companies operating in complex sectors like energy. Its varying safety requirements can complicate risk management for these organisations. Here’s an example of how one company might adopt a standardised Safe System of Work to ensure consistent safety protocols across various operational areas.
In the energy sector, some companies operate both renewable and non-renewable energy facilities. Due to this variability, many companies adopt a standardised SSoW framework to coordinate different safety practices.
One such example is a standardised SSoW document that outlines key principles and practices that can serve as a benchmark for a company’s specific SSoW systems. This document provides an extensive approach to workplace safety, offering a unified philosophy and clear guidelines for implementation.
The document includes:
- A sample SSoW policy that companies can adopt.
- An SSoW philosophy to guide safety practices consistently.
- High-level principles that are applicable across various operational contexts.
- General provisions to ensure adherence to these principles.
Additionally, the document provides instructions for applying these principles to several operational aspects, including:
- General workplace safety.
- High voltage (HV) and low voltage (LV) electrical systems.
- Mechanical equipment.
- Equipment operation.
- Work area demarcation and equipment identification.
It also outlines specific work control and safety documentation requirements and clarifies the roles and responsibilities of personnel in implementing SSoW principles. Key terms are defined to standardise understanding across teams, enhancing clarity.
This SSoW document is designed for use by trained and competent personnel alongside industry- and company-specific guidelines that address particular hazards, such as arc flash or electrocution risks. With its high-level structure, the document provides a common foundation, which companies can adapt and integrate with their existing safety protocols to ensure comprehensive workplace safety.
What Is the Difference Between a Safe System of Work and an SOP?
While both are important for workplace safety, Standard Operating Procedures and Safe Systems of Work serve distinct purposes. SOPs function as detailed roadmaps, guiding workers through specific tasks with precise, step-by-step instructions. These procedures ensure consistent performance while maintaining compliance with industry regulations and company standards.
A Safe System of Work takes a broader view. Instead of focusing on individual task completion, it examines the entire work ecosystem to identify and address potential dangers. This comprehensive framework digs deeper - analysing methods, predicting risks, and implementing protective measures before problems arise.
Think of an SOP as a detailed recipe for task completion, while an SSoW acts more like a shield, safeguarding the entire operation through systematic risk assessment and prevention. Where SOPs ensure tasks meet established standards, SSoW anticipates and neutralises hazards before they emerge.
How Is a Safe System of Work Different from a Risk Assessment?
SSoW and risk assessments serve distinct purposes but are closely related. An SSoW is a structured method that identifies hazards and specifies control measures for safe task execution. It essentially serves as the roadmap for safely completing a task.
A risk assessment, on the other hand, determines if an SSoW is necessary by identifying hazards and determining the level of risk. This evaluation helps decide whether additional safety protocols, like an SSoW, are required to manage those risks effectively.
Building a Culture of Safety and Excellence
A Safe System of Work is an essential framework for managing operational risks and protecting workers. Organisations can create a safer, more productive work environment if they combine thorough risk assessments, clear procedures, consistent training, and ongoing monitoring. Participation of employees in the Safety System of Work process promotes a collaborative safety culture.
Companies like Data Solar CX set a high standard, integrating comprehensive Safe Systems of Work within their commissioning services. With a focus on streamlined project execution, regulatory compliance, and enhanced on-site safety culture, Data Solar CX emphasises the value of proactive safety measures and rigorous QA/QC standards, driving operational excellence across high-stakes environments.