What Is Quality Control in Engineering? A Beginner's Guide
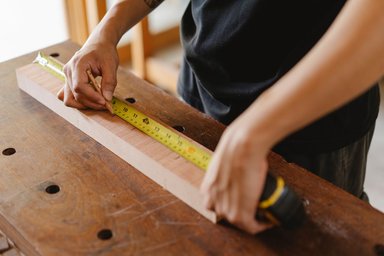
What is quality control in engineering? It is the set of processes, inspections, and checks to confirm that every project output meets the client’s standards, adheres to regulations, and fulfils its intended purpose. Maintaining such quality standards is critical in engineering, where even minor deviations can lead to safety risks, budget overruns, or reputational damage.
High-quality work can build a strong reputation, foster customer loyalty, and keep costs under control. On the other hand, poor quality undermines trust, causes rework, and wastes valuable resources like time and materials. By applying rigorous QC measures, engineering companies remain efficient, maintain clear communication, and promote safer workplaces, ultimately raising standards across an entire organization.
What Is QC in Engineering?
Quality Control in engineering is the system that ensures deliverables meet the client’s specified criteria. This often includes adhering to design parameters, regulatory constraints, environmental standards, and any other benchmarks set by the client, governing bodies, or industry regulations. Essentially, QC measures confirm that the end product fulfils its intended purpose safely and reliably.
The primary objective of QC is to spot and correct any inconsistencies before they become significant liabilities. In practice, engineers and project managers conduct periodic inspections, monitor ongoing work, and compare results against predetermined measures.
Any deviations from specifications are identified promptly, which lowers the chance of having to re-do entire project sections or deliver subpar results. Successful QC management keeps a project on schedule and within budget and strengthens client satisfaction. You can expect repeat business and positive referrals when your team delivers consistent quality.
What Is the Difference Between QA and QC?
In discussing quality within engineering, two related concepts often come up: Quality Assurance (QA) and Quality Control (QC). While they share a common goal of ensuring the final deliverable meets the highest standards, they accomplish it differently.
- Quality Assurance (QA): This focuses on creating a proactive framework to ensure quality is built in. QA activities might include establishing processes, defining requirements, implementing safety rules, and developing documented procedures that set a project up for success.
- Quality Control (QC): By contrast, QC is about verification. It involves directly inspecting and testing work output to see if it meets established expectations. If issues arise, QC procedures guide the team in resolving them as quickly and efficiently as possible.
DataSolarCX’s commissioning services illustrate both sides of the equation. The company sets strong guidelines and training programs before work begins, mirroring QA and then conducts on-site checks, thorough documentation reviews, and authorisation procedures, reflecting QC.
What Are the 4 Types of Quality Control?
Quality Control can be implemented in various ways, but four recognised methods appear across many engineering disciplines:
- Process Control
This involves monitoring and adjusting a process to maintain a consistent outcome. Engineers track key indicators such as temperature, pressure, or voltage to ensure operational stability. If a project involves the commissioning of a power facility, continuous monitoring is crucial for staying within safe operating conditions. - Acceptance Sampling
Rather than inspecting every single unit or component, a selected sample is evaluated to judge the entire batch. If the sample meets specific benchmarks, the batch is deemed acceptable. This is common in large-scale projects such as hyperscale data centres where full inspections could be too time-consuming or expensive. - Control Charts
In manufacturing and engineering settings, control charts help teams visualise performance data over time. Spikes or shifts in the chart indicate potential problems that require attention. Maintaining these charts can be especially useful for high-voltage commissioning tasks, where subtle deviations may cause major issues if not caught early. - Product Quality Audits
These are formal, often more in-depth inspections or evaluations of the finished product (or a major subsection of a project). Audits verify whether all specifications, industry regulations, and client expectations have been met. For instance, DataSolarCX’s on-site audits might involve documenting compliance, verifying authorisation standards, and scrutinising safety conditions.
Practical Steps for Implementing QC
When you’re setting up or refining an engineering quality control plan, consider these actionable steps:
- Set Expectations and Acceptance Criteria
Begin by defining the project’s quality expectations. Make sure everyone from engineers to subcontractors knows the desired result and the standards it must meet. These criteria could include regulatory guidelines, client-specific goals, and agreed-upon design specifications. - Develop an Inspection Strategy
Schedule inspections at various project milestones. This prevents issues from going unnoticed until the final stages. A vigorous inspection plan also lowers the risk of project overrun, as corrective measures can be applied immediately. - Create a QC Checklist
Without a universal checklist, each team or department might interpret standards differently. A streamlined checklist helps unify all stakeholders around a consistent set of criteria. By flagging oversights early, it bolsters communication, reduces mistakes, and ensures fewer reworks. - Fix Errors and Shortcomings
No engineering plan is flawless from the outset. Make sure enough resources and time are allocated for handling unexpected issues. Guided by a predefined QC process, quick action lets you resolve problems before they become systemic or cause major project delays. - Review and Analyse Outcomes
Take time to evaluate how each phase performed. Was there a particular recurring issue? Could a small process tweak prevent similar problems on the next project? Documenting lessons learned and circulating them among the team fosters a culture of improvement. - Communicate with Clarity
Effective communication ties all these steps together. Keep quality control front and centre when discussing project specifications, potential risks, or adjustments. Each engineer, manager, and consultant needs to remain informed about quality commitments and how they can help meet them. - Leverage Technology
Modern engineering often demands sophisticated planning, transparent communication, and streamlined execution. Automated checklists, digital dashboards, and cloud-based data sharing can offer the oversight needed for complex or geographically dispersed projects. Technology also provides a reliable record of inspections and actions taken over time. - Have a Backup Plan
Even the best strategies might encounter unexpected disruptions, supply chain issues, last-minute design changes, or staff turnover. A backup plan (or multiple ones) can prevent these events from cascading into major setbacks. Ensure to log these contingency strategies clearly, so everyone knows when and how to employ them.
Move Forward with a Robust Quality Control Strategy
Quality Control in engineering protects your investment, shapes your reputation, and ensures a safer, more predictable workflow. An effective QC plan lowers rework, improves team morale, and controls budgets by verifying each step, from raw materials and design specifications to final output. It also strengthens the trust clients place in your organisation.
For firms that aim to raise standards of safety, consistency, and performance, QC is part of an overarching strategy for success. Data Solar CX demonstrates this approach by combining robust engineering commissioning services, industry-leading safety training, and thorough documentation. Their dedication to clear processes and skilled teams shows how an integrated method of Quality Control and Assurance can produce reliable outcomes even in large, complex projects.
If you are looking to refine your engineering quality control plan or need expert guidance on commissioning and specialised safety training, consider reaching out to DataSolarCX. Our practical, results-focused methodology can help steer your projects toward consistent, measurable success.